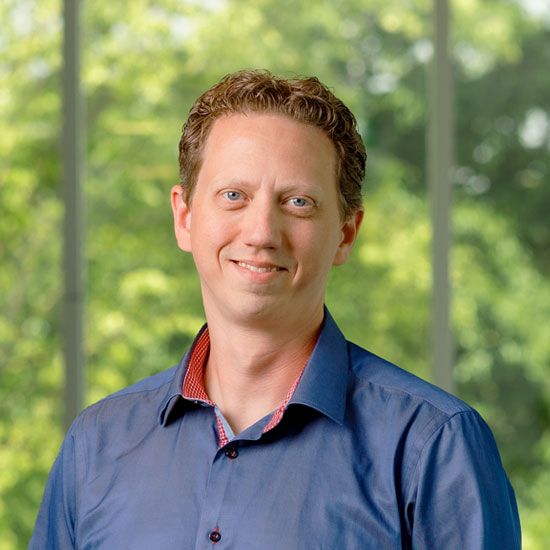
rapid choice of concept, robust implementation.
The contract required immediate action. We spoke to the Master of the Mint and carried out tests on the coins in the laboratory. Due to the limited timeframe, we opted to reuse available solution components where possible. We chose the concept based on several fast, simple tests. The immediate availability of components was also a key factor. A robust implementation was key to ensure reliable operation in Chile under conditions that were not known in advance. We tested sub-systems in parallel to be able to quickly build the machine. It was ready for transport within four weeks.
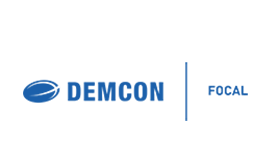
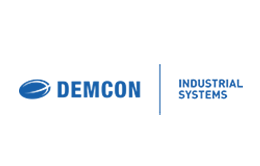
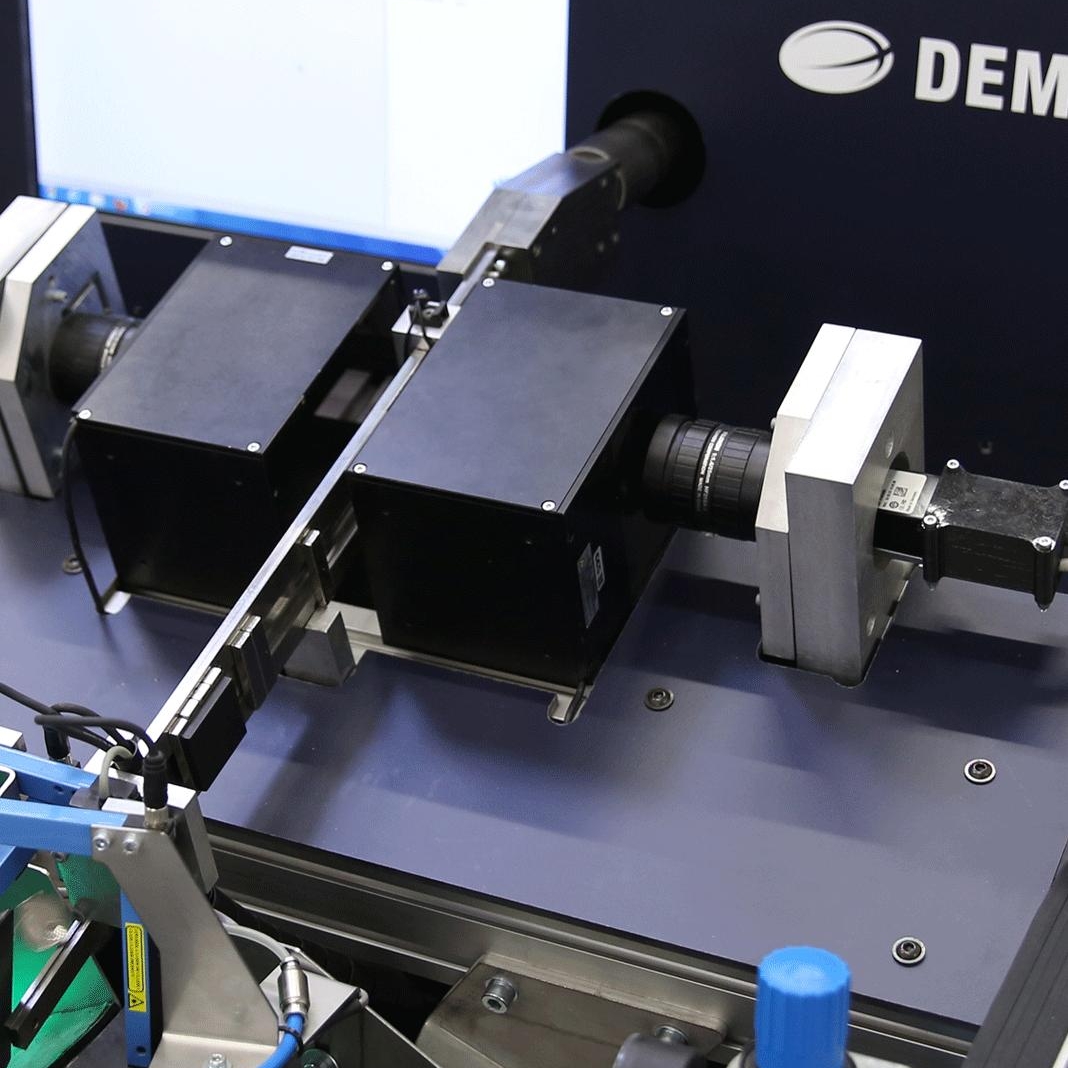.jpg)
complex vision algorithm.
Our biggest challenge was the complex, model-based vision algorithm, which in near real time had to detect a large variety of stains and make reliable decisions. We substantiated this with a thorough statistical analysis. To be able to immediately address any problems that might crop up, it was essential to be able to train the algorithm onsite. Ultimately, the machine continued to run at full capacity for over three months and inspected 40 million coins. The project was successful because the end-customer approved the inspection results without a hitch.
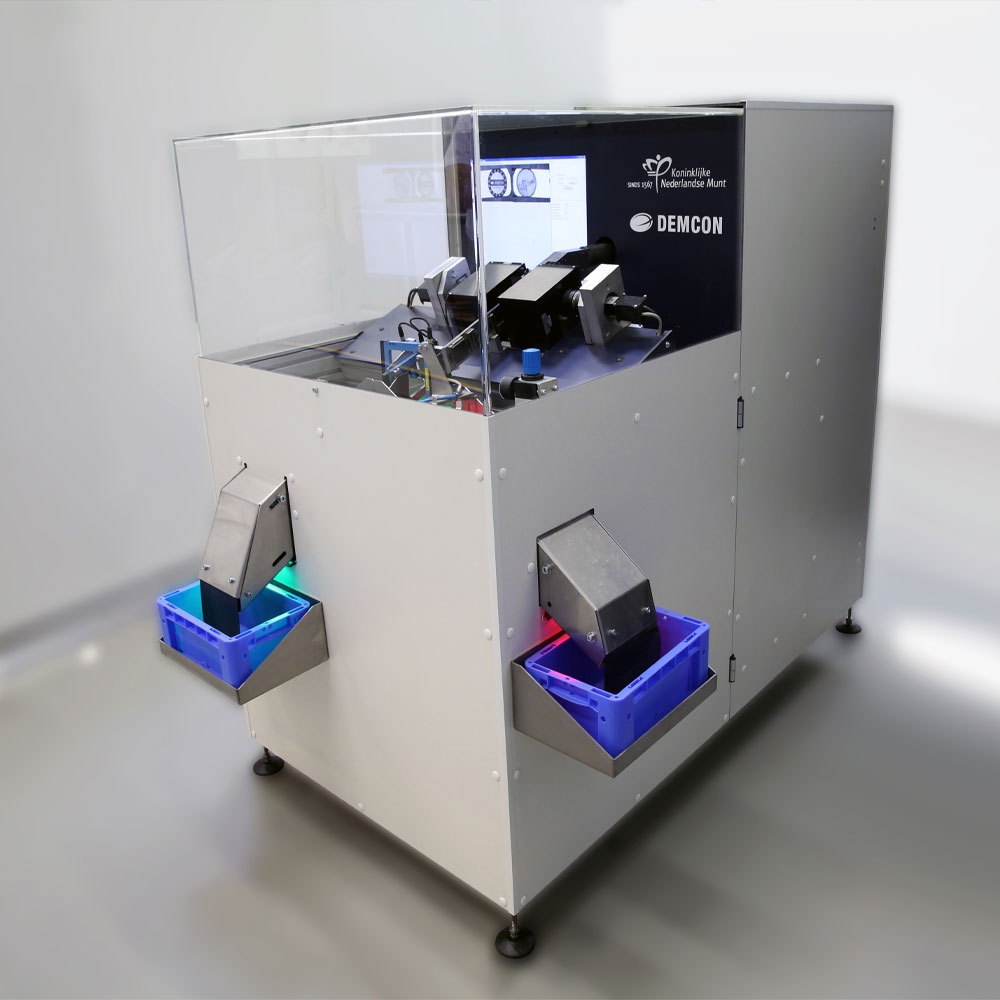
"our inspection of coins was 100% watertight."
Most importantly, the inspection of the coins was 100% watertight. ‘Approved’ had to be really approved and ‘rejected’ preferably really rejected, and that was successful. The Master of the Mint had never before seen such a machine that even detected stains he himself had not noticed. Due to our efforts – under severe time constraints – the customer was able to avoid a penalty.
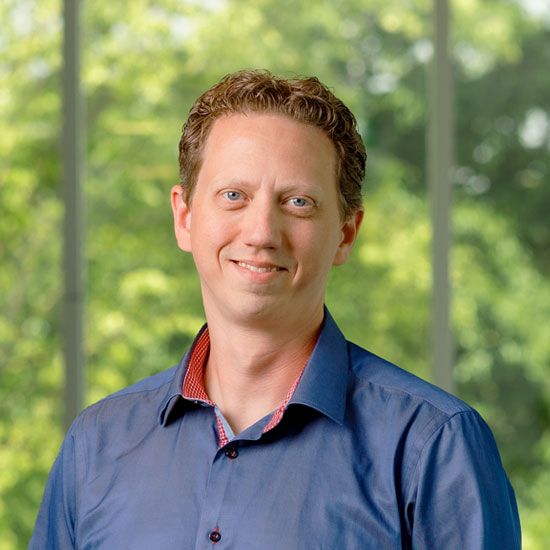